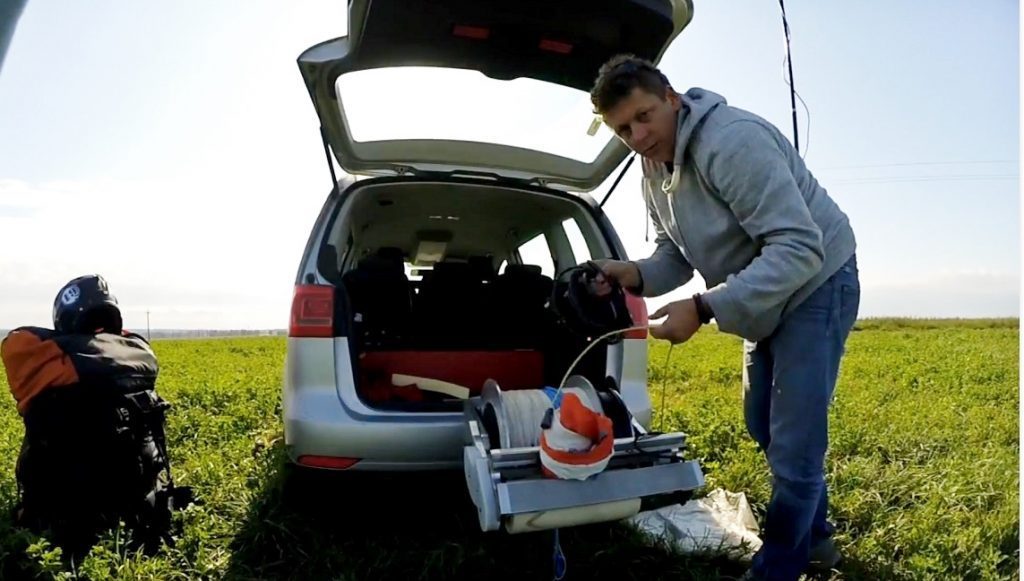
Andrey made himself his autonomous paragliding winch
In Belarus, no relief, so paragliders use the winch
Interview with Andrey by ROCK THE OUTDOOR
First, I would like you to introduce yourself and tell me your paragliding story in a few words
Hello, my name is Andrei Bresski. Google says that my name might be even of French origin derived from the name of the province of Bresse – who knows! However, I was born in Belarus and currently live in our capital city of Minsk.
I work in a private company as an engineer technologist, our company produces cushioned furniture like couches, armchairs, beds, and similar.Since I was a child, I was fond of DIY designing. Later I fell in love with aircraft modeling and I am still a big fan of it. Strangely, my love story with paragliding has begun in France. There was a period in my life when I lived and worked in Paris (around 2001 – 2010). I met friends who also dreamed of paragliding, and one day back in 2008 my French buddy purchased a second-hand paraglider of the past century for training and short flights. This paraglider has started my launch to the skies (see photo right). After that, I also have been practicing with more modern wings but that’s another story…
How did you come up with this idea of creating your own autonomous winch system?
Despite my rather long flying history, my pilot level remained at an average level, I simply do not have enough time for regular practice. There were several reasons for this. In 2010, I returned to my homeland. In Belarus, to my great regret, there are no mountains, not even small hills of at least 30-50 meters height! We can find forests, fields, swamps, ravines, uplands, but take off is only possible via a winch or a paramotor. We also have a very small paragliding community here. Thus, there is a small number of winches and access to them is not always possible at your first request. So you can understand that the desire to fly autonomously did not appear out of thin air.
I had a choice only between self-parawinching and paramotor. One day I found this youtube clip that gave me a hope of becoming independent (see video right). However, the price of this device was outrageous. Its technical characteristics also left much space for improvement. With the course of time, the elementary base of electrical devices in the field of electric transport has highly improved. Thanks to our Chinese friends, the prices also turned to be more acceptable for painless experimentation.
How did your project mature at the time of design (choice of parts and materials)?
Around 2015, I seriously thought about building my own winch. At that time, I have not found any related projects in the Internet and YouTube except Skynch. Therefore, I explored various types of already existing active winches: hydraulic, scooter and other exotic options. Jumping ahead, I will say that the design of my winch is not the most optimal by weight-dimensional characteristics for an autonomous winch.
Can you describe the main production lines of your system and the final choice of materials?
While designing the winch, I calculated the necessary power required to fly in the worst-case weather scenario. In summary, these conditions are the following: if there is no wind, the average traction developed by the winch is 80 kg at a speed of winding 10 m/sec. It corresponds to about 8 kW of mechanical power. Hence, the electric motor must yield electric power of at least 10 kW. Because 10kW is quite a high target, I needed a motor at a higher voltage to reduce the currents. I decided to take the engine of supply voltage around 75V. As for the battery, I took cheap lead batteries, because I did not care about minimizing the weight. I could simply carry the batteries in my car, so why not to save some money.
You know that the trollers are trained as a winch because it is technical and it presents risks. What are the precautions to use your autonomous winch?
In order to make the winch autonomous, I needed to satisfy at least these two conditions: (a) the winch should be able to provide the required traction and (b) be controlled remotely. First, to ensure traction, it is sufficient to stabilize the motor current at a predefined level. This can be handled by a controller for electric transport which has a limiter of maximum motor current. As a result, at full throttle, you will get constant traction independent of the cutting speed. The current limit level will set the thrust level. Jumping forward, I can say that such a controller has several usage limitations with the winch. The most serious limitation is the strength of the wind, because if the wind causes the wheel to stop, the controller will suddenly turn off the traction, which is not very pleasant, especially at a low altitude. At a sufficient height, you just give a second command and continue climbing if the wind allows.
Second, for remote control I used a modern low-cost RC control as it has a good noise-free channel range. Finally, having collected all these modules together and combining them with an auxiliary microprocessor like Arduino, I could create a control for the winch.
It was also important for me to release the pilot from unnecessary wires, as the pilot has already got too much of them. Another issue to avoid is extra control over the winch. Therefore, I created only one button to control the winch – pull on/off – apart from the power on/off buttons of the RC module. At the start, the electronics smoothly increases traction helping the pilot to raise the wing, then after 10 seconds it reaches full traction.
Of course, it would be convenient if the winch could automatically wind the cable after the pilot’s disengagement. This function is already available, but is not very stable. Therefore, I prefer to not use it until I fix all the issues. Currently, the cable has to be rewound under the pilot’s control.
What do the pilots who saw the system and those who have already used it think?
My winch has been tested by several pilots from the local community. Since all our pilots possess extensive experience of flying on winches of various designs, their feedback was very valuable. All the pilots evaluated the winch very positively. The electric winch feels like an active hydro-winch, but the traction is even softer according to all the pilots. Overall, they liked it very much.
You have published 5 videos. These are different versions? What are the weak points and improvements that you have made?
These are not 5 versions, but five videos about the same winch. Basically, these are different tests performed while I was improving the look of the winch. As for improvements implemented, there were mainly electronic and software bugs fixed. Apart from that, I would like to refine automatic cable winding as I mentioned above.
If, after testing, your system is reliable, do you plan to market it? If so, do you have a price range?
I never planned to commercialize my project. For me, this is a part of my hobby so that to be able to practice paragliding autonomously. I understand that the current winch version is still very raw both mechanically and electronically. This is OK for DIY usage, but not enough to go to market. Overall I spent about 2000 USD on everything, not counting my work effort. This winch turned out to be pretty heavy. Also, the controller for electric transport imposes a number of restrictions on the use. I will not mention each of them in detail, as they require too much technical explanations. To date, there is a commercial offer from a guy about whom I wrote above.http://miamiparagliding.com/. Their product is of simple design and is ready to use – so winch enthusiasts can take a note of that. However, I am not sure what exactly is in the electronic part of the winch and how well it works.
I will make a small announcement: after the people found out about my winch, a group of people in Russia started building their own electric winch. Most importantly, their goal is to build a specialized controller for the winch electromotor, which will eliminate all those bugs that I currently struggle with. If they succeed, I will start building a second version of my winch, twice as light and smaller in size. I have already designed everything, the material is purchased, it only remains to wait for the controller to be complete by this enthusiast group. Probably this project will be commercialized, but it is too early to talk about pricing now.